Water reuse is becoming an important part of water resource management. As this trend grows, it is vital to understand how to choose the most cost-efficient water reuse system – both in terms of the initial capital investment and operating expenses over the long term. Research from Xylem now shows how customers can achieve an optimal solution, depending on different treatment methods, reuse purposes and plant sizes.
Starting in 2012, Xylem and IVL Swedish Environmental Research Institute began an extensive research project on water reuse system design. The mission was to understand the costs of building water reuse plants, their operating expenses over 20 years, and how to deliver the most environmentally efficient solution.
Aleksandra Lazic, Senior Process Engineer of R&D Treatment at Xylem, has been involved in the research project from the beginning. She says that one important measurement and decision tool when building or retrofitting a sustainable water reuse plant is the plant’s life cycle cost (LCC). The LCC, which this article focuses on, includes capital expenditure (CAPEX) and operational expenditure (OPEX).
Finding 1: For a water reuse system, operational expenses can cost more than capital expenses in the long term
The research first involved a pilot study at Hammarby Sjöstadsverk looking at eight different treatment lines. Then the researchers did full-scale modeling of four different effluents in plants of three sizes: 20,000 PE, 100,000 PE, and 500,000 PE. The modeling, based on market conditions in Spain, showed that for plants larger than 100,000 PE, OPEX is the largest fraction of the overall life cycle cost, not CAPEX.

“This is really interesting and important because many people focus only on the initial investment costs, on how much they pay today,” Lazic says. “In fact, the research shows that the initial capital investment is not an adequate indicator of a sustainable economic solution. You need to look at the long-term operating costs to determine your full life cycle cost. With this information, we can show customers interested in sustainable solutions how they can achieve the lowest cost over the long term for their particular plant size.”
Finding 2: The size of the plant matters when determining the most cost-efficient, sustainable solution
“The size of a plant plays a huge role,” Lazic says. “One example is for agriculture reuse, where you can get the same effluent quality from two different kinds of equipment, either a dual-media filter or a disc filter. If a customer with the smallest plant size in this study, 20,000 PE, is only interested in finding a cost-efficient solution, then the disc filter line is acceptable – although it uses chemicals. As the size of the plant increases, however, we saw that the dual-media filter led to the lower life cycle cost.”
“We have created a matrix of information around life cycle costs,” Lazic says. “Based on the size of a customer’s plant, regional requirements, and their interest in sustainably lowering their costs, we can help them find a water reuse system that meets their needs.”
Finding 3: The secondary treatment step costs the most to build and operate
When building a treatment plant for water reuse, in addition to conventional wastewater treatment steps the plant also needs tertiary and disinfection steps. The research shows that the largest initial investment, mostly due to civil cost, and long-term operating costs come from the secondary treatment step.
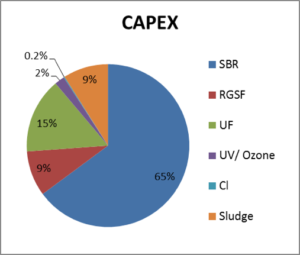
“In order to understand which part of the treatment process is most responsible for costs, we looked at each step, from the preliminary step to disinfection and sludge handling,” Lazic says. “We did this to learn where we need to focus our R&D efforts so we can decrease the overall life cycle cost. What we found is that the secondary treatment step, SBR, has the largest fraction of the cost in a water reuse system.”
SBR represents 65 percent of the total capital investment for a plant, followed by sludge handling and rapid gravity dual-media filtration both at 9 percent, and UV at 2 percent. This means that improving water quality to the reuse level increases the LCC by only a few percent. In addition, when looking at the operating costs of a plant over 20 years, energy consumption represents 56 percent of total costs. Half of this energy is used by SBR.

“We recommend optimizing secondary treatment to achieve the best treatment sustainability,” Lazic says. “These findings have also led us to continue our work on the secondary treatment step, so we can decrease its footprint and energy consumption. For example, we have used this research to decrease the footprint of our ICEAS SBR solution by 15 percent, which decreases CAPEX by 10-15 percent.”
Xylem has also developed a process controller for its ICEAS SBR solution called OSCAR. Due to the work done at Hammarby, additional control modules were developed that have decreased energy consumption by 20 percent, and OPEX by 10-15 percent.